|
 |
PMC (Patent 6,860,297) Restoration Method (PMCap)
Pressure Boundary Repair Component for Piping and
Pressure Vessels
|
|
 |
- The PMCap
repair
method provides users with a quick and cost effective alternative to
flush patch and weld overlay repairs.
- The PMCap
is welded
to the outside surface of a component using a full penetration weld and
replaces the encapsulated pressure boundary.
- Code compliance is restored without
requiring
degraded area removal. Cutting of pressure boundary, foreign
matter intrusion, and exposure of vessel internals to the environment,
is eliminated.
- The PMCap
includes
a corrosion allowance, or can be constructed of corrosion resistant
material or with a corrosion resistant liner.
- PMCaps
are designed
and constructed to ASME Code rules and are supplied as ASME
code-stamped components. The complete package includes hardware,
partial data reports, shop fabrication drawings, material test reports,
and certified calculations.
- Please refer to our Fitness
for Service
software and unique Metal Loss Evaluation Charts (MLEs) for
evaluating local thin areas prior to performing repairs.
- Total hardware and installation
costs using the PMCap
Repair Method are significantly less than those associated with
traditional flush patch and weld overlay methods.
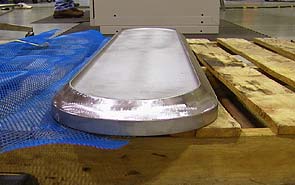 |
|
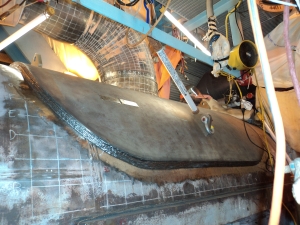 |
As-Constructed Obround PMCap |
Installed Split PMCap |
|
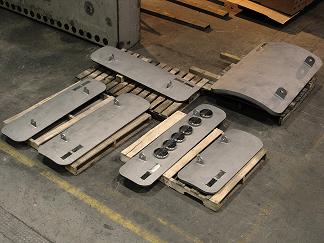 |
|
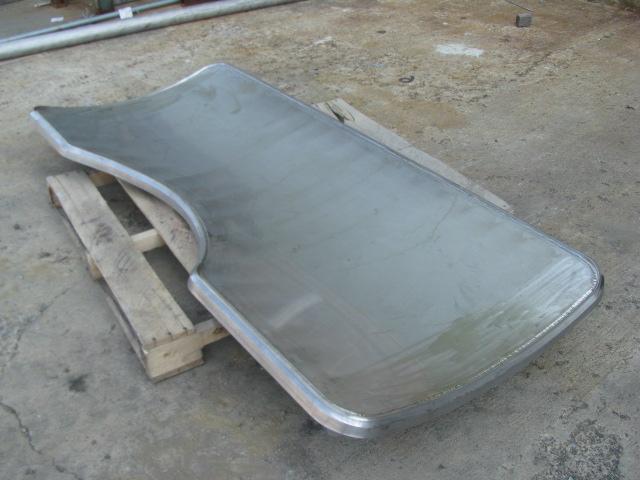 |
PMCaps
– Ready for Shipment |
As-Constructed Split PMCap
(Underside View) |
|
|
 |
The PMC Restoration Method
has several
advantages over the traditional “flush patch” or
“weld overlay” methods of repair, and alleviates many
negative aspects. Advantages of the PMC Restoration Method
include but are not limited to:
|
 |
The PMC Restoration Method:
- does not require cutting out
local
degraded
material areas
- requires minimal preparation
of pressure
retaining material. In contrast, “flush patch
repair” or “weld build-up repair” methods may require
significant weld preparation
- generally smaller than flush
patch.
Flush patch must match surrounding material thickness. PMCaps
may be attached to sound material of any thickness that meets code
requirements.
- does not require, but allows
use of,
weld
joint backing strips in the attachment weld between the
pressure retaining item and the PMCap.
- eliminates exposure of
personnel to
lethal or
hazardous fluid contents such as chemical, gas, or radioactive
fluid contents of a pressure retaining item.
- eliminates potential damage
to internal
parts
of pressure retaining items such as damage to tubes of heat exchanger
- eliminates potential
intrusion of
foreign
materials into the internals
- simplifies any required
hydrostatic or
pneumatic testing of pressure retaining item since pressure
boundary is not breeched
- is not limited to a specific
geometrical
shape
and may be constructed to most any regular or irregular shape including
but not limited to round, obround, square, or any combination of the
these shapes. May be split to encapsulate nozzles.
- generally only requires
surface
examination
of attachment welds, however, full volumetric examination of
welds is possible
- satisfies all
ASME Code criteria,
National
Boiler Inspection Code, API-610 Pressure Vessel Inspection Code,and has
been accepted by State Jurisdictional Authorities and major insurance
carriers
|
|
|